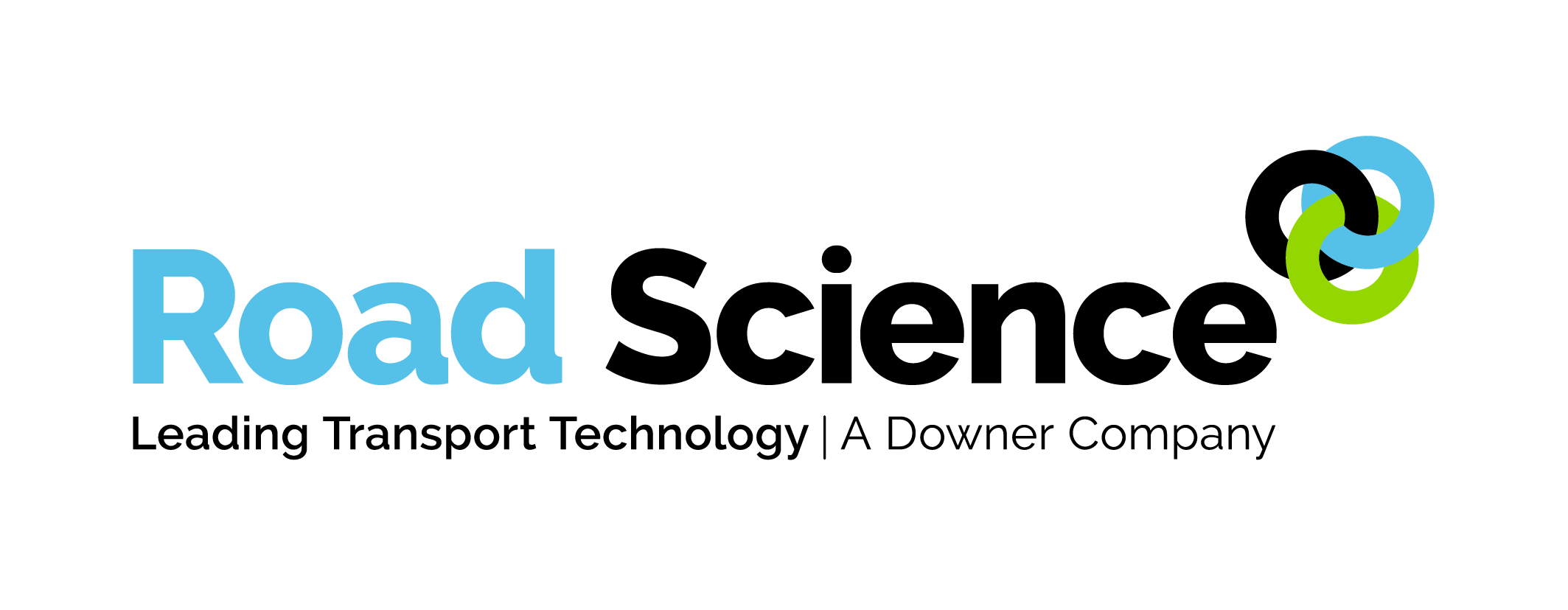
Road Science is committed to advancing the pavements industry through innovative products and services that are developed and supported by engineering science.
Working with chain of world-class manufacturing plants and storage facilities for asphalt, bitumen, emulsions and polymer modified binders through-out New Zealand.
Their supply chain is further supported by New Zealand’s largest bitumen tanker fleet, they also provide a range of pavement design, technical and consultancy services. They have created a unique focus on technologies to deliver superior road & pavement solutions for longer lasting roads across every NZ situation.
Road Science is committed to advancing the pavements industry through innovative products and services that are developed and supported by engineering science.
Working with chain of world-class manufacturing plants and storage facilities for asphalt, bitumen, emulsions and polymer modified binders through-out New Zealand.
Their supply chain is further supported by New Zealand’s largest bitumen tanker fleet, they also provide a range of pavement design, technical and consultancy services. They have created a unique focus on technologies to deliver superior road & pavement solutions for longer lasting roads across every NZ situation.
What are your maintenance goals and how is MEX used to help achieve these goals?
We wanted to create a robust, easy to use but flexible preventative maintenance system to replace our old historic paper-based system. Road Science uses a combination of MEX features that create a seamless experience for the user. These include:
Regions
All four sites are all included on our single MEX platform, but using the ‘Regions’ module means that the different sites only see their own assets and work. By having the different sites on the same database however, copying preventative maintenance templates over is quick and easy.
Inspections
We also utilise the inspections (asset audit) format extensively, which means that multiple assets can be handled in a single work order in a way that makes sense for our operators. We occasionally use the standard (known as the ‘tick and flick’) work order format, but it is under 5% of our preventative maintenance work (and breakdown work orders).
MEX Mobile App
Road Science uses the MEX app on mobile devices that have their own roaming data, so information is added to MEX in real time on location. Using the inspections format in conjunction with the app not only means that assets can be added and removed to work orders ‘on the fly’. It opens up options to add comments and photos against individual assets whilst minimising the amount of work order traffic in the system. This also provides a one-click access to detailed asset history, as well as customizable prompts which trigger when specified results are entered.
What benefits have you seen since implementing MEX, can you think of an example where you feel MEX has led to a return on investment?
Road Science uses the MEX app on mobile devices that have their own roaming data, so information is added to MEX in real time on location. This means that photos can instantly be added to work orders via the mobile device, and requests for further work with all the relevant information can be logged instantly.
This had reduced the time spent logging, notifying and following up on work and increased our productivity. Over time, the productivity gains will continue to grow (as well as reduced costs from a more robust preventative maintenance programme) exponentially as our database history grows.
You were recently involved in App Beta testing, tell us a little bit about your experience with this & working with the MEX Development team.
Sylvie Kerr, Systems Support Super User was a BETA tester for the new app, and advocated for a seamless experience for those using the inspections format. The Development Team really took on her feedback, and she is really excited with the end result. Anyone who uses inspections format work orders in their MEX system will be enjoying the streamlined functionality of the new app.
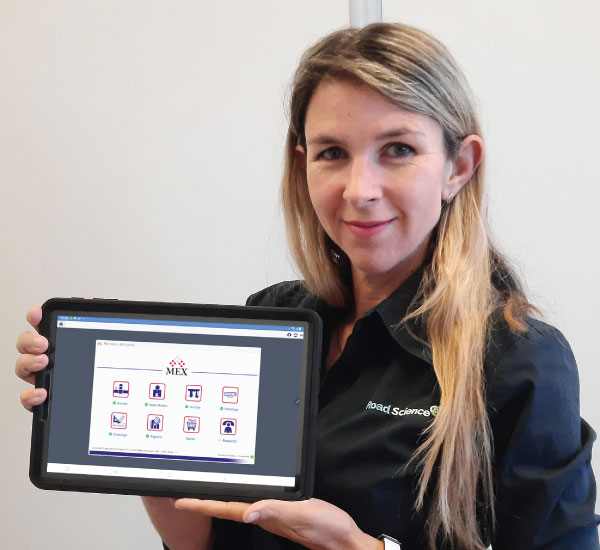
What advice would you give to someone looking to implement MEX?
Use MEX’s bulk data upload functionality to originally populate your asset tree. This process ensures your asset tree is constructed in a logical way, and any issues with the information is flagged by the system during import. I would also use bulk data uploads to enhance existing asset records.
I would strongly recommend using the inspections format from day one. Aside from advanced detail capture (comments and photos by asset) it gives a great deal of flexibility to modify the general workflow of your MEX preventative maintenance programme.
The questions and answer sets that live in the background behind the inspection format get used again and again, and modifying or adding to your maintenance programme using this format is seamless.
I would also recommend that end users learn to use MEX via the app. Those performing maintenance should be able to access everything they need via the app (if configured correctly) and it encourages regular engagement with preventative maintenance tasks and correctly capturing checks in the MEX database from day one.
Don’t bother with printing out work orders. It’s 2021. Just go paperless! Contractors can have their own portal if they need it.
Contact the MEX Sales Team today for more information on the Road Science Case Study or call + 61 7 3392 4777
This Case Study was last updated: 23/02/2021 08:02