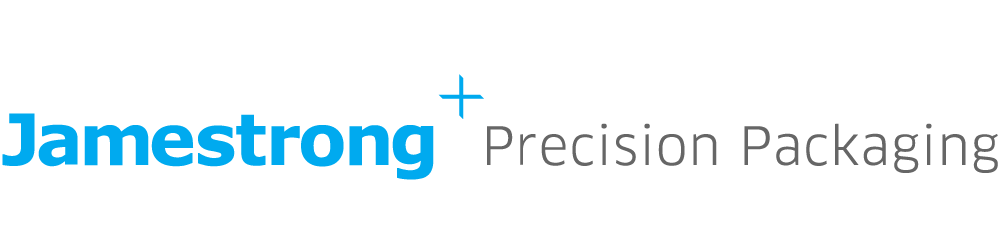
Jamestrong Packaging is a leading packaging supplier in the Australasian region with the head office located in Melbourne and 4 manufacturing facilities located throughout Australia and New Zealand. Jamestrong Packaging operates across three distinct divisions - Food cans (human food and nutrition), Aluminium Aerosols and Tinplate Aerosols. Offering a broad range of innovative packaging solutions to meet the varied and changing needs of customers.
What are your Maintenance Goals?
To have our maintenance planned and experience minimal breakdowns.
How is MEX Used?
MEX is used across several of our sites to aid in the planning and executing of maintenance work. We have MEX Regions that allows each of our sites to have their own independent maintenance operation whilst only having access to their corresponding assets.
We use MEX to manage and maintain our manufacturing equipment with the aim to minimize downtime and keep production at optimal levels.
All our assets at each site are listed in MEX, we enter Work Orders for any maintenance that’s required and include any parts that are needed. This process has allowed us to get a complete picture of our assets and manage them effectively.
What benefits have you seen since implementing MEX, can you think of where MEX has led to a return on investment?
Our Preventative Maintenance schedules in MEX have resulted in regular accurate servicing of our equipment which has led to a reduction in our downtime. A direct return on investment.
MEX is an excellent tool for displaying maintenance records, PMs and work completed to our external auditors.
What advice would you give to anyone in your industry looking at implementing MEX?
MEX is a great tool when used correctly, it’s easy to get help and support from MEX when required, and there is always training available to help you with the software.
Contact the MEX Sales Team today for more information on the Jamestrong Packaging Case Study or call + 61 7 3392 4777
This Case Study was last updated: 03/08/2017 10:08