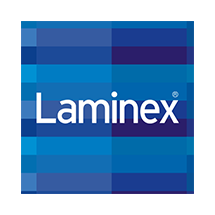
The Laminex Group is Australia’s leading supplier of modern laminates, quality engineered stone, timber panelling and much more. Laminex has six manufacturing sites across Australia and our maintenance processes are very asset intensive. We started the MEX implementation because each of our manufacturing sites had/have a different CMMS. Additionally, a couple of those applications are aged and unsupported, e.g. not compatible with Windows 10.
What are your maintenance goals?
From an overall business point of view, our main goal is to maintain high asset availability and reliability. We recognised the need to move to a single enterprise wide CMMS so maintenance could be improved as a whole. Before implementing MEX, each of our sites worked with a different application which made us work/develop unique process flows. Our planning and scheduling processes were different at each site where we realised that there is no consistent approach to maintenance or reliability.
As a result, our first goal is to remove the risk of aged and unsupported CMMS failure. In addition to this, we aim to develop consistent and standard maintenance management processes across the entire business.
How is MEX used to help achieve these goals?
MEX was chosen as the best fit for Laminex due to its modern interface and high level of support. Whilst implementing the system, MEX helped us remove the risk we are facing of system failure. It also challenged our perceptions of maintenance and steered us toward the world’s best practices. By adopting the processes established by MEX, we have been pushed to quit our old ways and align each manufacturing site to a consistent and standard maintenance approach.
I personally feel that MEX is allowing us to setup a strong foundation that we can build upon and ultimately achieve our availability and reliability goals.
Our Engineering Team are assisting you with a project, can you describe what this work entails?
As part of this project, we are developing an interface between MEX and our ERP. This will allow us to use MEX Stores and the Purchasing Module alongside our current system. The MEX/ERP Interface will remove manual transactions and eliminate double handling of data between the two systems.
The MEX Engineering Team supported us every step of the way where their help and guidance were essential for us. They assisted us from the go live process, testing, data transfer and issue resolution.
Can you rate the level of service you received?
Excellent, their support and help are greatly appreciated. MEX and Laminex just started this journey, however I personally feel we are working more as partners than just service providers.
Contact the MEX Sales Team today for more information on the Laminex Group Case Study or call + 61 7 3392 4777
This Case Study was last updated: 04/10/2019 09:10