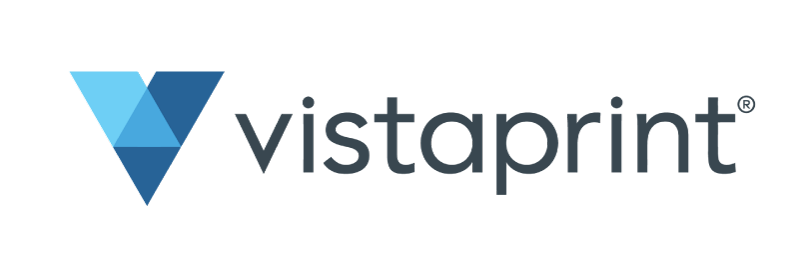
Vistaprint is an online supplier of printed and promotional material and marketing services to micro businesses and consumers, specialising in printing on demand products. Vistaprint applies the principles of mass production (Lean Manufacturing) to printing, using presses and processes of industrial printing for short-run commercial printing. Vistaprint’s proprietary process involves multiple software components, and the management of multiple production components, in an end-to-end production workflow from “click to ship” with production facilities in Windsor – Canada, Venlo - Netherlands, Melbourne - Australia and Bhiwandi - India.
How the MEX Maintenance Software is used?
To promise on time, high quality and in budget customer service, we rely on MEX to deliver on its promise to us. Having a functional and flexible CMMS ensures consistent and effective maintenance management and practices. In general terms, MEX is critical to our manufacturing performance by helping us to plan, schedule and improve our level of maintenance excellence.
We use MEX to manage all our assets from site, to building, to floor and right down to a component level. All our critical equipment is linked to its supplier details, PM policies, Work Order History and associated spare parts Stores inventory. We currently have 305 assets in our register, 146 active Preventative Maintenance Policies and 1657 items in our Stores Catalogue. Since June 2010, the installation has captured close to 6000 Work Orders that have been completed and moved into History. Extending MEX to the “shop floor” via the Requestor’s module has increased the “return on investment” by capturing remote requests 24 hours a day, seven days a week with over 60 active users contributing to more than 1200 requests actioned by our maintenance team.
The MEX Reporting Module and KPI’s helps us to track our success which in turn allows Vistaprint to keep our promise and commitment to our customer while ensuring that our high Safety, Quality and Financial expectations are met and/or exceeded.
An example of our accomplishments in managing our maintenance, this year Vistaprint Australia was awarded a bronze medal from the Shingo Institute at Utah’s State University for Operational Excellence.
Right from the start the keys to our success have been establishing a clear and long-term vision to be the best at what we do by assembling a talented team of people and giving them the right tools for the job. MEX has been a part of our organisation from day one.
Contact the MEX Sales Team today for more information on the Vistaprint Case Study or call + 61 7 3392 4777
This Case Study was last updated: 17/11/2014 08:11